Ceradyne / 3M Seattle manufactures high tech glasses for a variety of industries, including electronics, semiconductors, and renewable energy.
The company continues to use a 4th Dimension lab management app we developed for them decades ago. The solution has evolved from a single purpose Purchase Order system to a multifaceted application used to assist in various quality management related functions. The original purchase order function has long since been subsumed by an SAP implementation, but the lab management, QMS document management, and discrepancy reporting functions continue to play a critical role in insuring the production of high quality, standards-compliant products for 3M Seattle’s customers.
As a part of its manufacturing process, the glasses being melted are tested for a variety of attributes like density, softening point, and particle size, and the test results are entered into the 4th Dimension lab management app. The 4D app has the key role of evaluating each test to determine if the results are within specifications and facilitating the appropriate process if discrepancies are found.
Recent modifications to the 4D app allow lab staff to be alerted more quickly if the trend in test results shows a potential issue. Use of Plotly, an open source javascript library for graphing, allowed us to quickly integrate more flexible control limit charting than the application was previously doing. In addition, the application integrates tightly with the user’s email accounts to alert different groups of staff of different potential discrepancy situations.
While making these changes, we re-factored the Lab test data entry interface to use the newer Listbox object in 4th Dimension, rather than the old Subform object. The Listbox object is easier to work with and creates a more modern look. This will make future user interface changes significantly faster to implement.
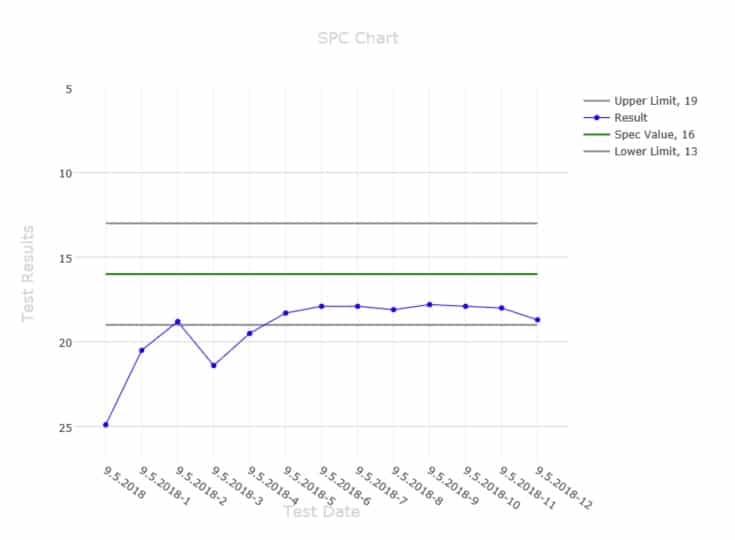
A key advantage of a custom application like this lab management system is the ability to quickly react to changing business circumstances and modify the software to suit new requirements. Had 3M Seattle been using an off the shelf solution, the ability to quickly make needed changes would have been more limited.